Calibration is the process of adjusting and verifying the accuracy of a measuring instrument against a known standard. In the case of fixed gas detectors, calibration is essential to ensure that they provide accurate and reliable readings of the gas concentration in the environment. Without regular calibration, stationary gas detectors could show erroneous readings, either underestimating or overestimating the presence of harmful gases.
The process of calibration
Calibration of stationary gas detectors is a delicate process that requires specialized skills and appropriate instrumentation. It usually involves the following steps:
- Instrument preparation
- Comparison with a reference standard
- Adjustment
- Verification of accuracy
Before starting the calibration process, it is important to ensure that the instrument is clean and in proper condition, then it is exposed to a known concentration of calibration gas to compare its readings with those of the reference standard. If the readings do not match the expected value, adjustments can be made to align them. After adjustments, the instrument is tested again to ensure that it gives accurate readings.
Frequency of calibration
The purpose of the tests is to check the proper functioning of detectors installed in the field. In European Community countries, gas operation tests and calibration procedures for gas detectors are required by current regulations and defined by EN 60079-29-2.
The periodicity of maintenance must be defined:
- by the type of instruments installed in the field
- by the risk level of the installation area
The guidelines for our gas detectors are:
- quarterly verifications for installations with level 1 emissions (Zone 1)
- semi-annual verifications for installations with level 2 emissions (Zone 2) or unclassified areas
- annual verifications for installations in Zone 2 or unclassified area where IR technology detectors are present
Entrust Sensitron with periodic maintenance
Our gas detection systems have different maintenance requirements depending on the gases detected and the applications in which they are placed. Scheduled maintenance ensures the efficiency of gas detection systems resulting in the safety of workers and environments.
Entrusting periodic maintenance to our team means extending the life cycle of the instruments with an impact on both operating costs and the environment.
Our products
Learn about Sensitron gas detection systems, consisting of gas control panels and gas detectors. These are some of the possible solutions.
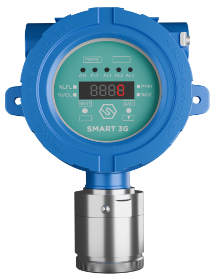
SMART 3G D2
Suitable for detecting flammable substances, toxic gases, refrigerants and oxygen in classified areas.ATEX, IECEx and SIL2/3 certified.
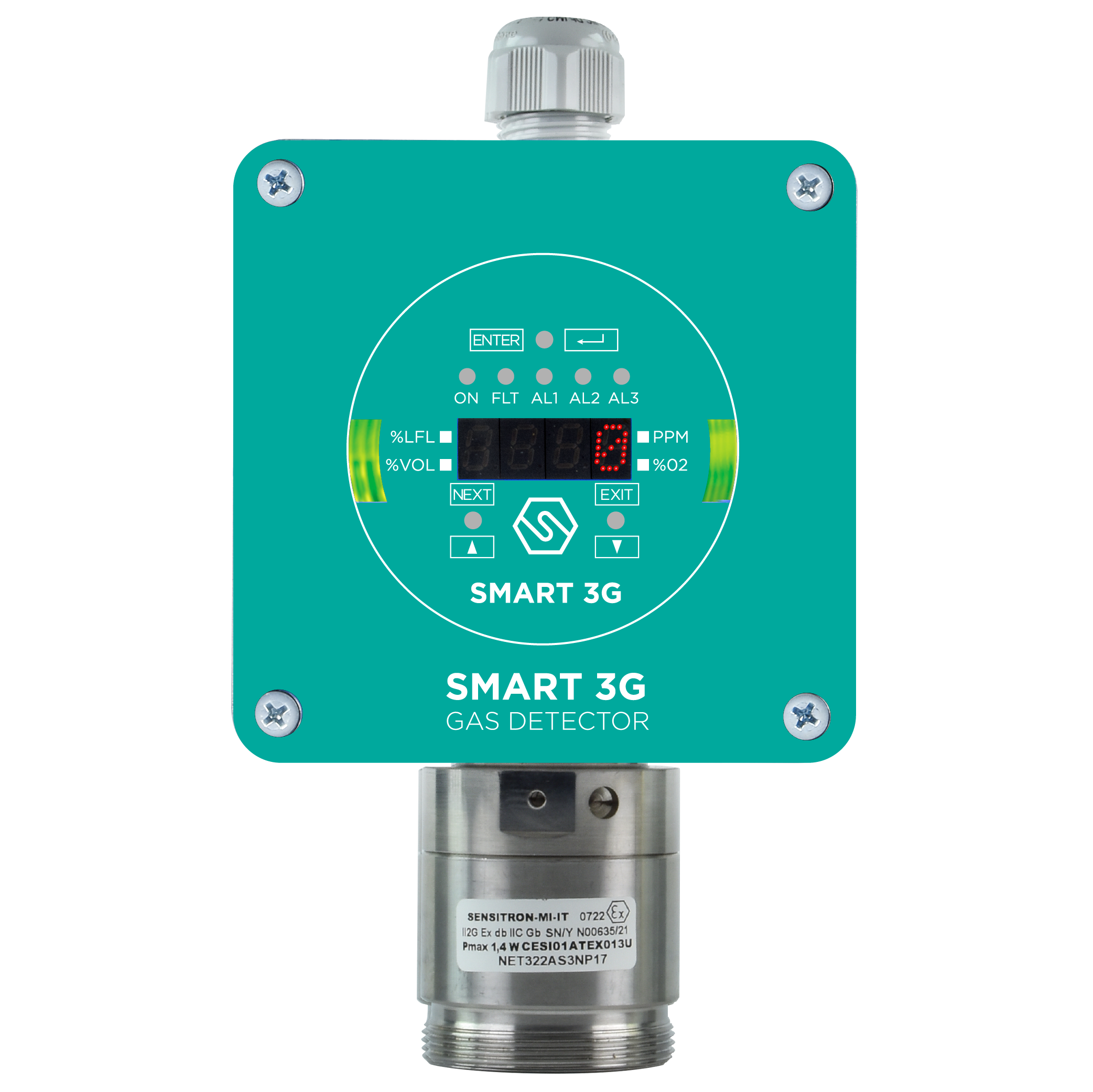
SMART 3G D3
Suitable for gas detection in classified areas, ATEX, IECEx and SIL2/3 certified, allows for non-intrusive field calibration.
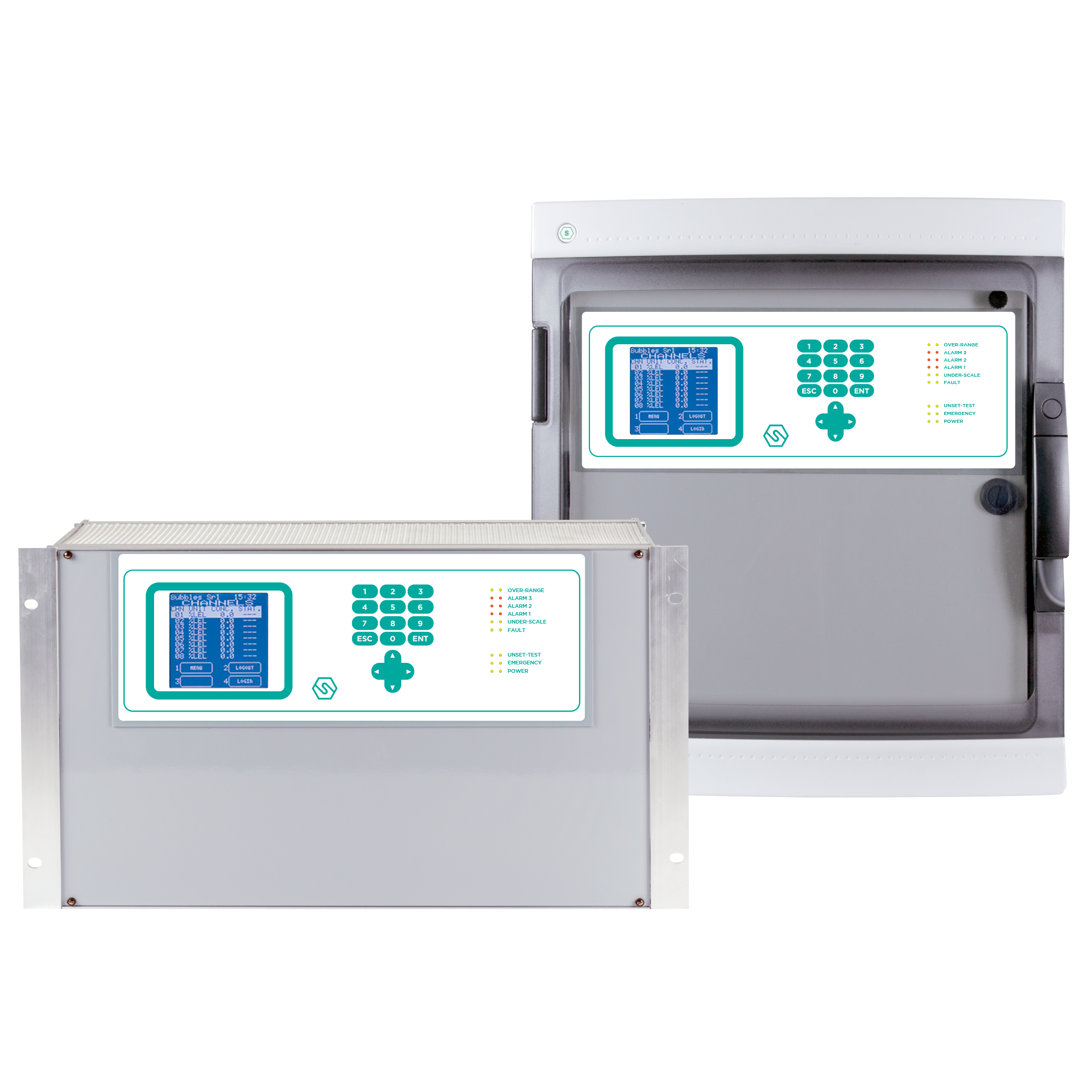
MULTISCAN++S1/S2
Designed to meet the widest market demand for flexibility, they allow the management of up to 264 detectors. ATEX and SIL certified.